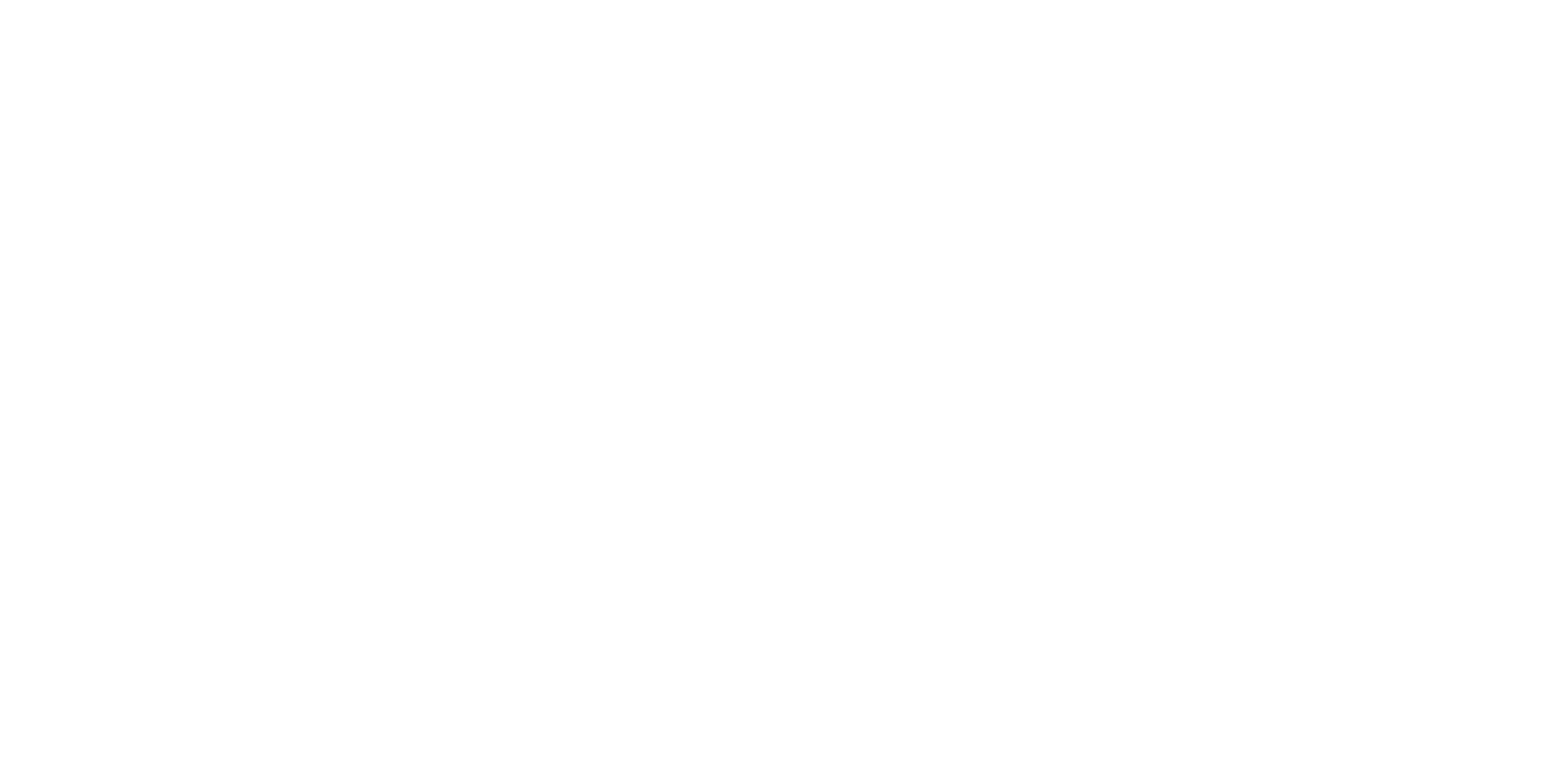
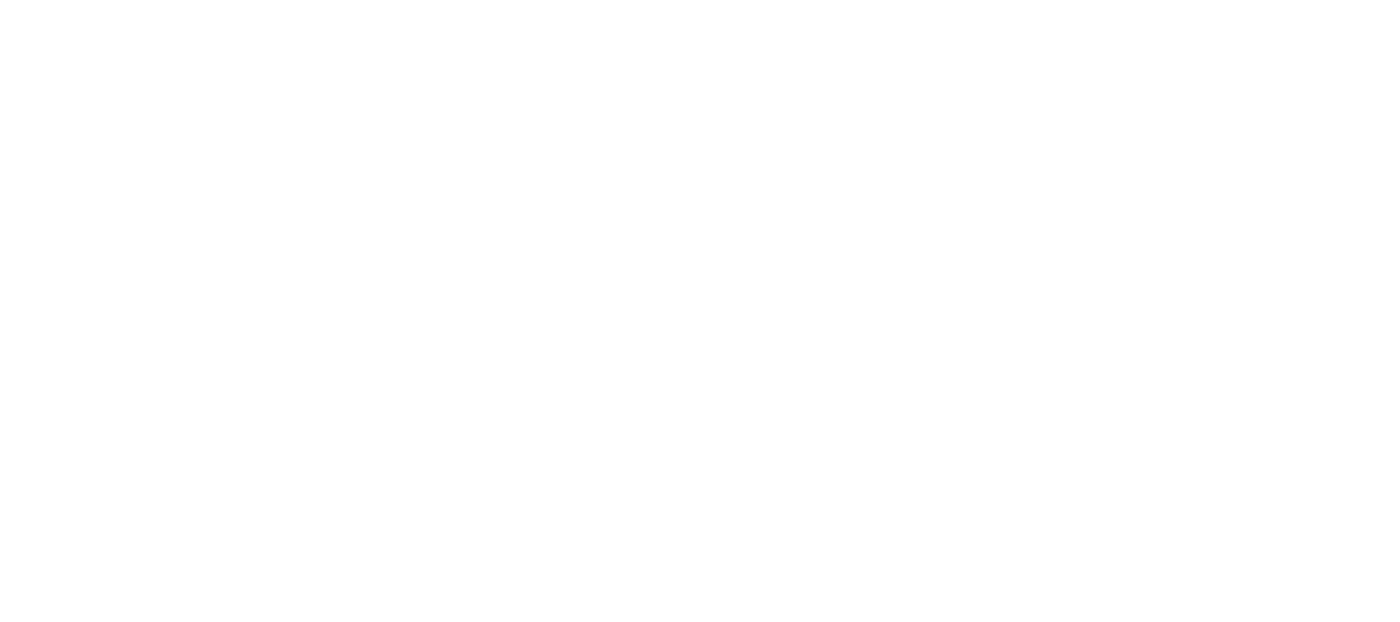

Choosing a Quality Management System
Please Select contact form.
Top Considerations
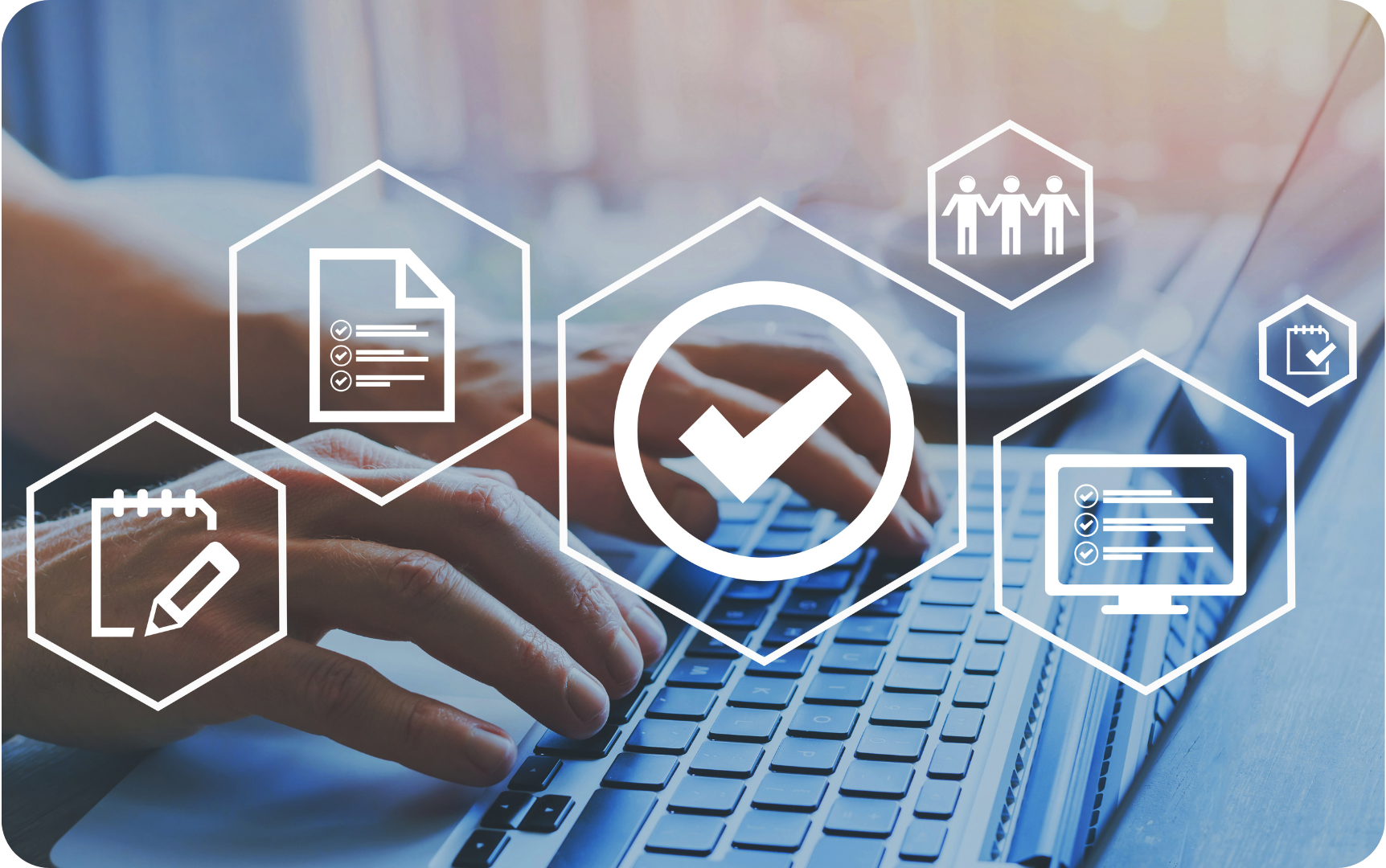
When considering implementing a new Quality Management System (QMS) for your company, it can be challenging switching to a new system despite the fact that your current one is complicated, fragmented, and offers little visibility or control.
The best QMS systems available today will, in actuality, not only satisfy your needs for quality management, but will also help the organization achieve goals that go beyond quality. These cross-organizational goals can, for instance, include making your processes themselves more agile or reducing the workload involved in using and maintaining them.
The following factors should be taken into account as you compare the various QMS software vendors to find a system that will be truly beneficial to your business. Look for the elements below in your search for the best Quality Management System for your organization.
What advantages does a Quality Management System software offer?
Consistent products: By achieving greater consistency in project activities, you can increase effectiveness by better managing time and resources.
Productivity level increase: By using proper evaluation techniques and improving employee training, you can raise your productivity level.
Less rework: Using the right procedures that guarantee prompt corrective actions are taken on the occurrence of defects can help you minimize rework resulting from warranty claims.
Improved financial performance: By strictly adhering to the requirements of quality standards and regulations, you can improve the financial performance of your product in the market.
Harmonization of regulatory requirements: This aids in the organization of CAPAs and gives you guidelines for improper deviations and the linking of production records.
Market share growth: This is possible thanks to quality management software, which offers appropriate risk and cost management for projects as well as development-based prospect identification.
Implementing best practices and improving processes: Using quality management software can help you cut costs, maintain consistency, and make sure that production is occurring within the baseline of the schedule.
Enhance documentation: It enables you to comprehend document-related systems and their requirements so that processes and activities are easily available and recordable.
Which Quality Management Software Trends are Popular Today?
Cloud-based: Quality management software now makes use of “the cloud” as a crucial asset across all industries, giving managers access to new advantages like process visibility and simple system integration across the supply chain.
Omni-channel communication: The QMS software now makes use of mobile technologies, giving stakeholders throughout the supply and production chain real flexibility, real-time communications, and system access from anywhere.
Data analytics: Quality management software is now presenting a thorough audit trail of assets and activities across the company and beyond using data analytics, all through system integration.
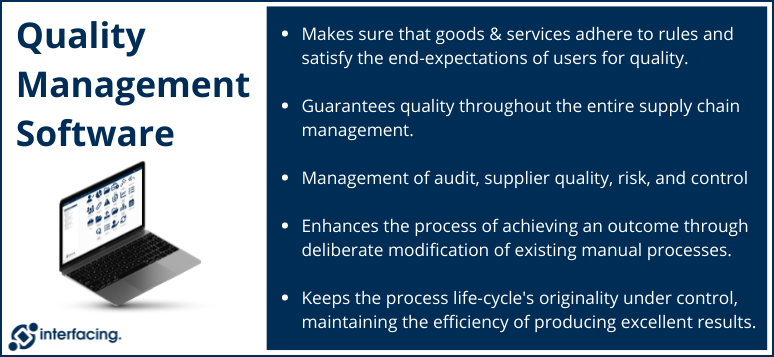
Key Considerations When Vetting QMS Software
These criteria will assist you in staying focused on the objective, which is to select a new Quality Management System that is easy to understand and use, makes the best use of your time and resources, and has the value-added capabilities you require.
Spend less time maintaining and switching between deteriorated document control and quality management modules. The best quality management software combines document control, quality data, and quality processes into a single, integrated system.
Applies the Current Technology:
Companies across the board are investing in cloud-based solutions due to their robust capabilities, ease of use, and configurability when compared to on-premises solutions. Refrain from using antiquated technology that hinders rather than helps your quality team succeed.
Ensures Collaboration:
Internal employees, as well as outside suppliers and auditors, are all included in quality processes and document control systems. Invest only in a system that enables remote access and collaboration between authorized users.
Is Simple to Use:
More than just annoying, a poor user experience wastes time, encourages manual workarounds, hinders data collection, and reduces process visibility. Invest in a system that is so simple to use that even infrequent users can log in and start working right away.
Places You in Charge:
Expect best practices for data security and complete access control to be built in. For multinational corporations, the ability to strike a balance between enforcing international standards and allowing for local autonomy when necessary is also essential to a successful global QMS.
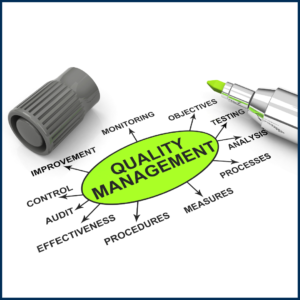
Localization is useful because it allows the user to create local copies and then tweak them, instead of having to re-map that manufacturing process for each country. Localization is also beneficial when processes are similar, but have slight differences caused by various factors: political, legal, geographical, social, etc. The localized copy should also retain its relationship with the source process (the process from which it was derived from), making management easier across location or product and service. Benefits Risk Management: To direct and support quality management activities, a modern QMS system should include embedded risk management tools. It is important for your QMS to have the ability to complete risk assessments, to assign risk mitigation controls, and to manage the ongoing lifecycle. Not only is risk management important to protect against disaster strikes, but by integrating controls into daily operations you can ensure that quality standards are met, and customer satisfaction is maintained. Additionally, there is nothing greater than the cost of “non-compliance”, hence, comprehensive risk and process transparency is a necessity to comply with laws and regulatory requirements such as Sarbanes Oxley, Basel iii, IMF, HIPAA, FDA, ISO 15000, among others. Keep Scale with Your Business and Pace: The regulatory, supply chain, and corporate complexity of today cannot be kept up with by on-premises systems that update infrequently. Any new system should be flexible enough to adapt to changing business requirements and should update frequently throughout the year. Your QMS ought to be a growing asset rather than a money pit. Focused on Customer Success: Do not settle for dial-in implementation and customer support from your software vendor. Look for vendors who regularly assess and enhance the performance of their products, have a proven track record of successful implementation, and base their performance on your success.
Glossary of Quality Management System Terms
Audit Management:
This software enables you to keep track of all audit-related paperwork and activities by recording both internal and external audits, monitoring the audits’ schedules and outcomes, and letting manufacturers assess the auditors’ efficiency.
Change Control:
Manage the individual pieces of information, assign owners, and ensure governance through approval cycles, and change requests. Including change request/change, lifecycle/improvement change. For example, integrated and embedded Approval and Governance workflows ensure strict control over the change of your records, including validation of changes, evaluation of impacts and highlighting changes.
Complaint Management:
Complaint is defined as a typical Quality Event type. Complaints management, therefore, is the aggregate of tools, processes, and behaviors the organization uses to collect, classify, analyze, and act on customer dissatisfaction, with both software solutions and human interaction with customers playing vital roles.
Risk Management:
It gives manufacturers a great platform to quickly assess risk by standardizing the risk assessment documentation and conducting analysis on recurrent problems in a single location.
Document Control:
It enables manufacturers to arrange all of their production-related documents, to trace all changes, including track change, version history, & audit trails. Additionally, teams dispersed geographically, are now able to connect, collaborate, co-author, proof-read, revise, comment and sign documents – all done electronically and securely within the system. Auto email notifications and read receipts support the systems expediting distribution process throughout the organization. Automatic document retention, printing, periodic reviews, and archiving are all in full compliance and controlled using USFDA 21 CFR part 11 encryption, making audits and quality inspections worry free.
Supplier Quality Management:
It consists of workflows for supplier qualification, scorecards for suppliers, and tools for tracking supplier issues. These tools assist manufacturers in choosing and keeping an eye on supply chain partners.
Employee Training Management:
It gives you a great platform for overseeing employee training by making sure that the necessary course materials are finished and keeping track of training activities.
Corrective and Preventive Action (CAPA):
This feature enables you to track and manage CAPAs by automatically routing corrective or preventive actions to the manager’s attention for approval or rejection.
Non-conformance Management:
Non-conformity is defined as a typical Quality Event type. Implementing and monitoring non-conformances and the effectiveness of each to avoid adverse business operations are made possible through eQMS. With an eQMS, each incident will be recorded with all associated action items tracked.
QMS Extensions:
It offers a great platform for automating the quality procedures that are unique to a given business, such as calibration and recall management.
Out of Specification Management:
‘Out of spec’ for short, is defined as a typical Quality Event type. This lets you make sure that lab result investigations that aren’t in line with expectations are reliable and efficient.
E-signatures:
It enables you to use an electronic signature to approve processes and reviews. One of the leading standards is 21CFR part 11, which is a must compliance for many industries. This allows you to make a compliant and paperless document effectively streamlining secure delivery to its recipient.
Analytics and Reporting:
It offers a great platform for creating, exporting, and sharing user-defined reports. It also enables you to perform risk analysis and improve project gap by utilizing the metrics you need.
Email Notifications:
This makes it possible for you to get immediate alerts about tasks, approvals, and adjustments to the production and supply cycle.
Role-based Security:
The ability to ensure that the appropriate personnel have access to the appropriate data at the appropriate times is made possible by role-based security.
User Dashboard:
Create highly customizable dashboards that users can edit and distribute throughout your company with the help of the user dashboard feature.
How Interfacing can Help End-to-End with a QMS Solution
We understand that the requirements placed on organizations in terms of compliance are very high and that ISO9000, ISO13845, ISO17025, ISO27001, SOC 2, FDA QSR and GxP is an essential part of that program. By using our solutions, including our eQMS module, your company gains the accountability and consistency that will give you a cutting edge over your competition. Our tools ensure full visibility from end-to-end, all the way from the creation and amendment of a regulation to the approval and revision of the content through to the update and retraining of employees for standard operating procedures (SOPs). We see the full lifecycle management as moving parts of a complete ecosystem and that’s why are unique approach that combines regulatory requirements, documents, processes, work instructions, and governance.
Combined with Interfacing’s industry leading digital Integrated Management System (IMS) its flagship product EPC, will significantly strengthen collaboration within IT development and operations. Your team will create, streamline, test, automate and deploy limitless workflows faster and with greater accuracy & efficiency.
Interfacing’s Enterprise Process Center® digital platform solution helps you maintain a complete library of:
- Processes
- Procedures
- Roles & responsibilities
- Risks & controls
- All regulatory requirements and standard controls
- Internal policies
- Aligned indicators (KPIs)
- Controlled indicators (Monitoring)
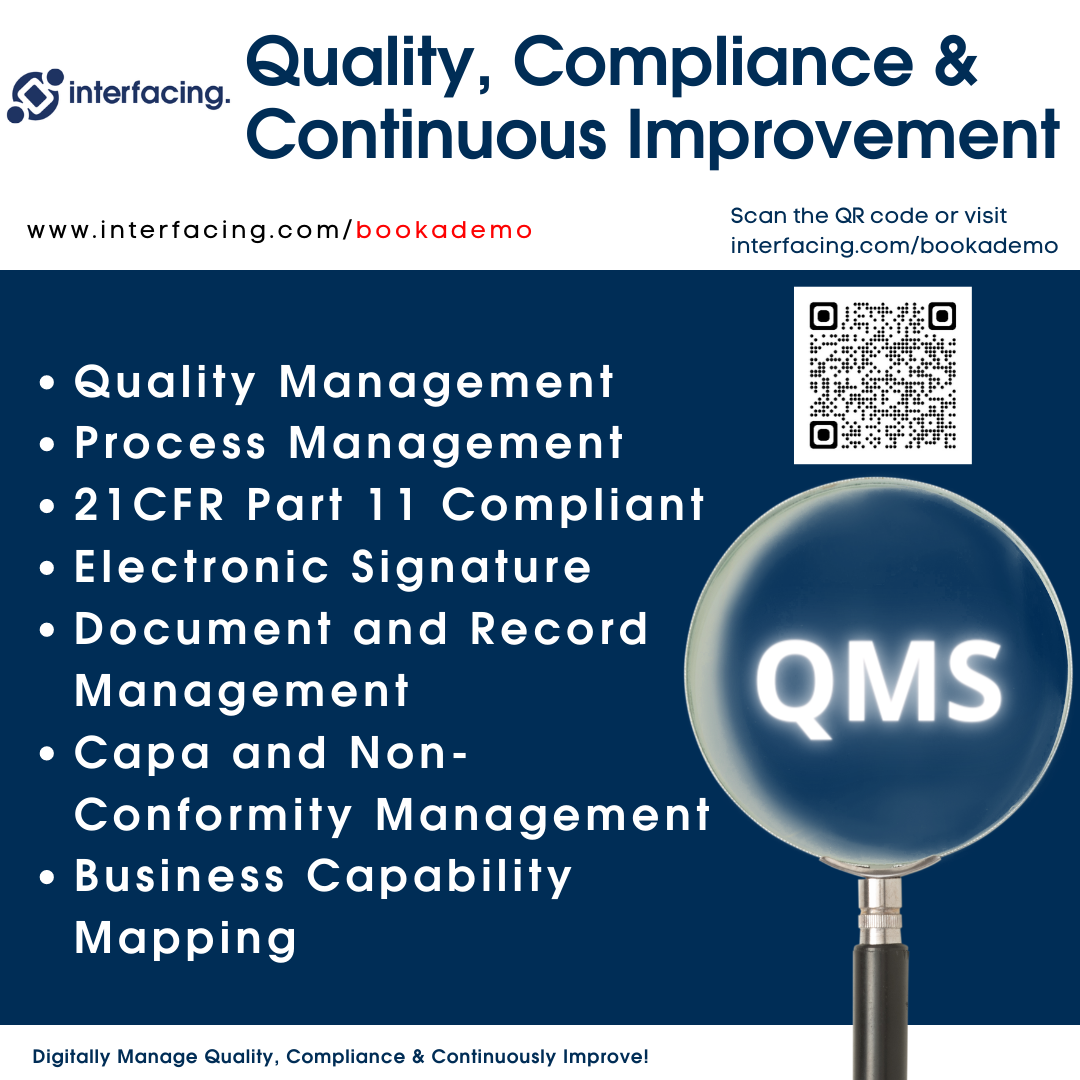
Why Choose Interfacing?
With over two decades of AI, Quality, Process, and Compliance software expertise, Interfacing continues to be a leader in the industry. To-date, it has served over 500+ world-class enterprises and management consulting firms from all industries and sectors. We continue to provide digital, cloud & AI solutions that enable organizations to enhance, control and streamline their processes while easing the burden of regulatory compliance and quality management programs.
To explore further or discuss how Interfacing can assist your organization, please complete the form below.

Documentation: Driving Transformation, Governance and Control
• Gain real-time, comprehensive insights into your operations.
• Improve governance, efficiency, and compliance.
• Ensure seamless alignment with regulatory standards.

eQMS: Automating Quality & Compliance Workflows & Reporting
• Simplify quality management with automated workflows and monitoring.
• Streamline CAPA, supplier audits, training and related workflows.
• Turn documentation into actionable insights for Quality 4.0

Low-Code Rapid Application Development: Accelerating Digital Transformation
• Build custom, scalable applications swiftly
• Reducing development time and cost
• Adapt faster and stay agile in the face of
evolving customer and business needs.
AI to Transform your Business!
The AI-powered tools are designed to streamline operations, enhance compliance, and drive sustainable growth. Check out how AI can:
• Respond to employee inquiries
• Transform videos into processes
• Assess regulatory impact & process improvements
• Generate forms, processes, risks, regulations, KPIs & more
• Parse regulatory standards into requirements
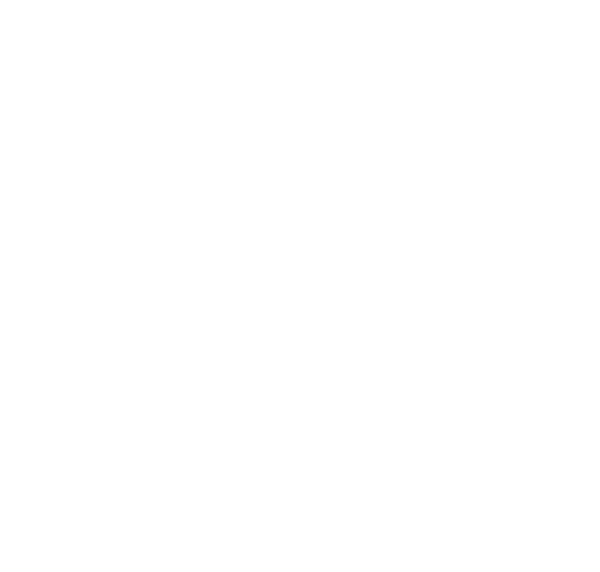
Request Free Demo
Document, analyze, improve, digitize and monitor your business processes, risks, regulatory requirements and performance indicators within Interfacing’s Digital Twin integrated management system the Enterprise Process Center®!
Trusted by Customers Worldwide!
More than 400+ world-class enterprises and management consulting firms
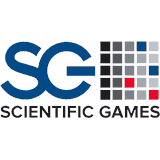
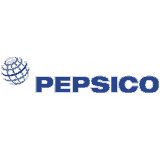
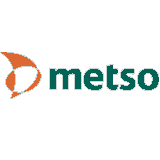
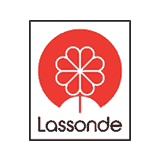
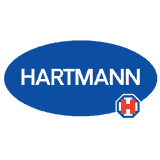
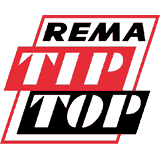
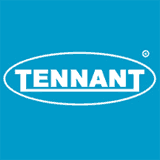
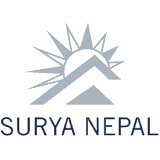
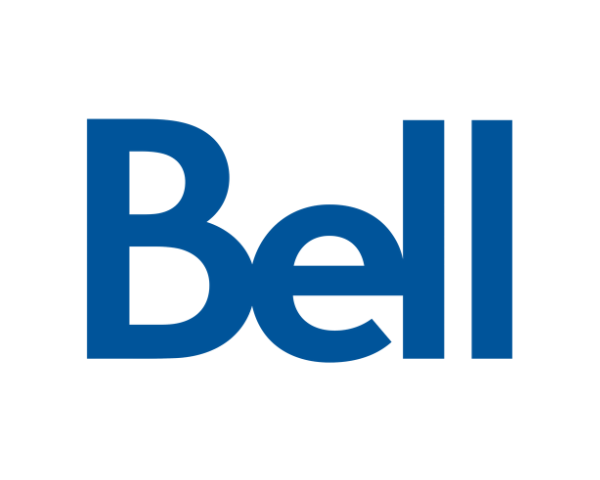
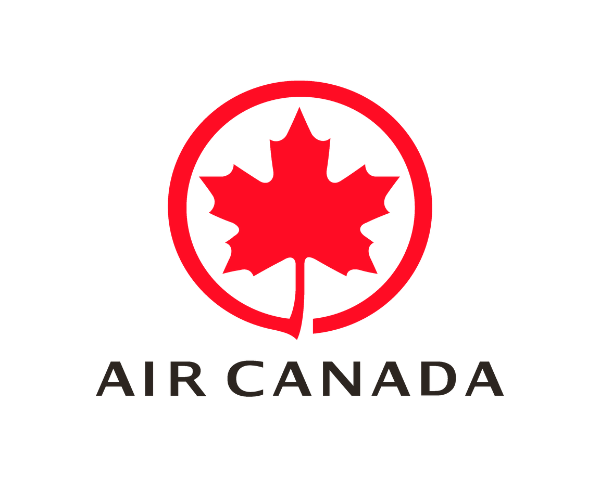
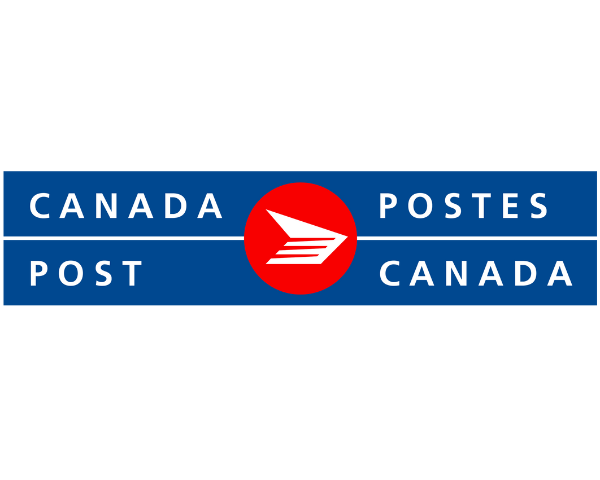
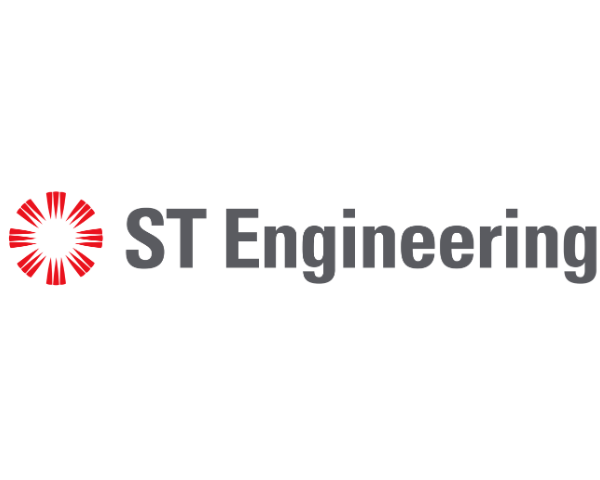

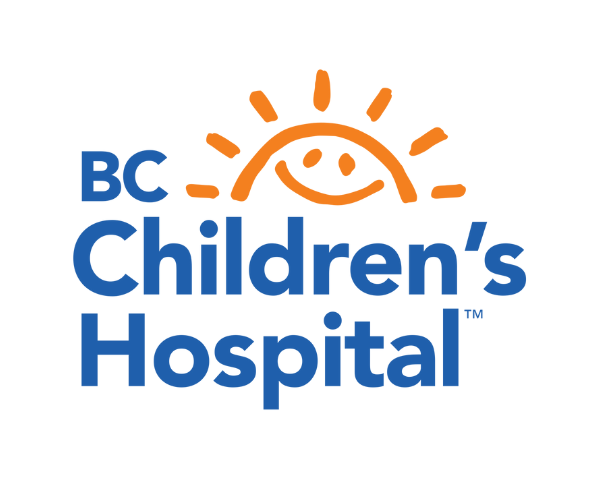
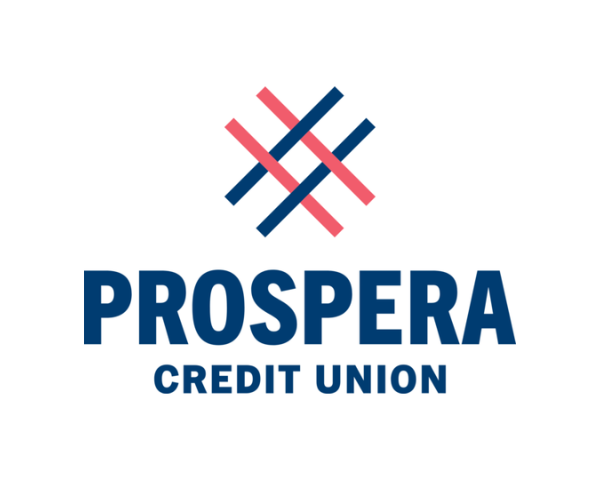
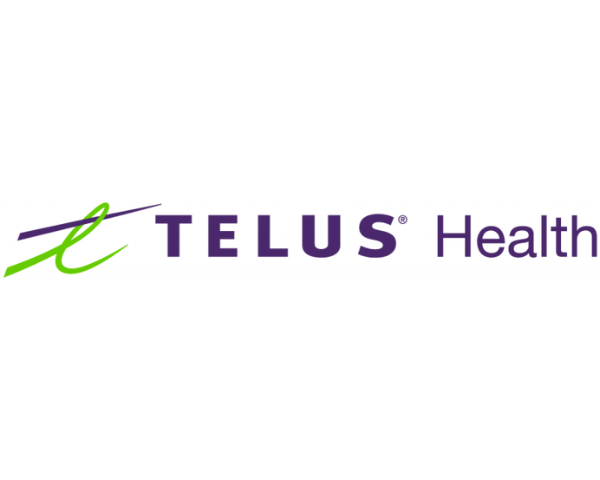
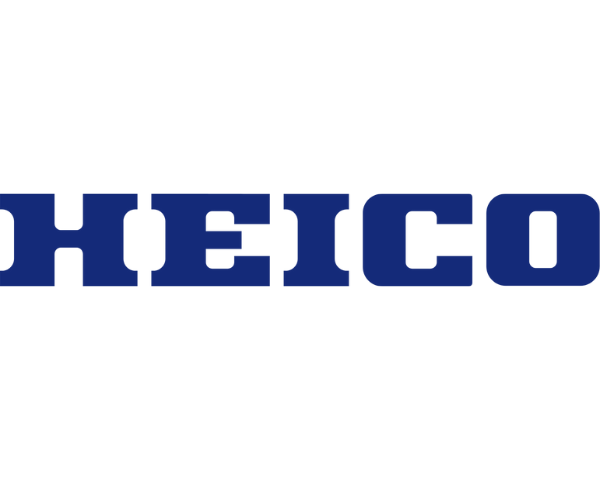
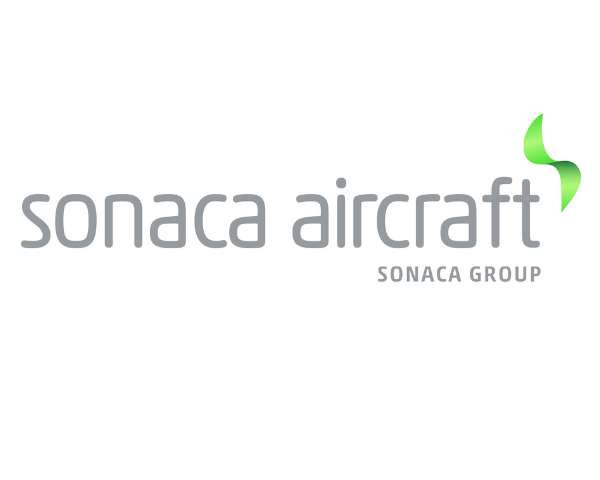
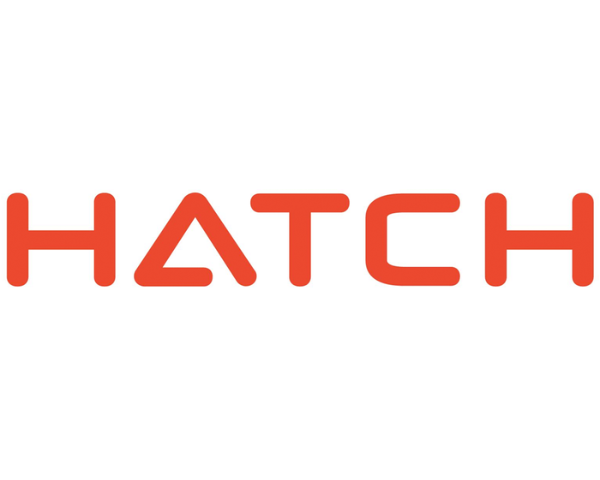
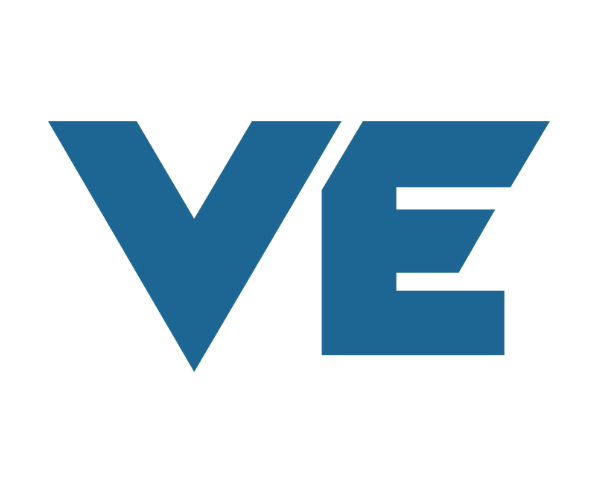
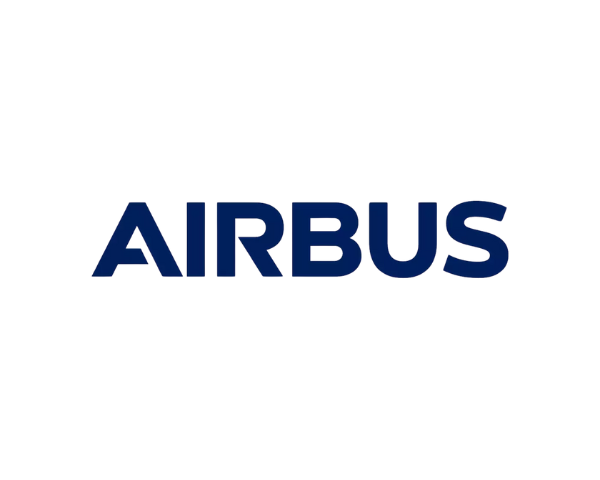
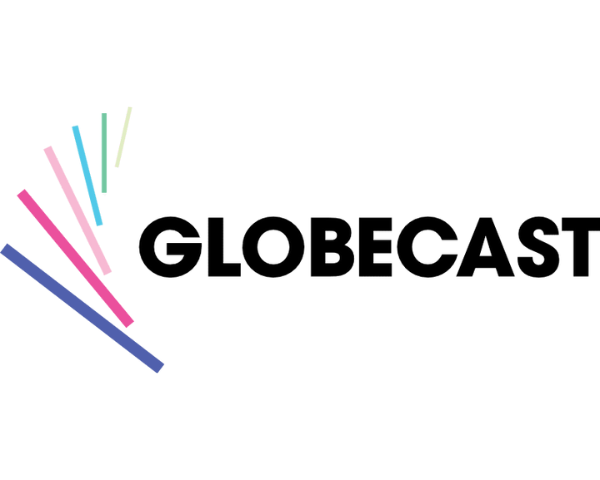
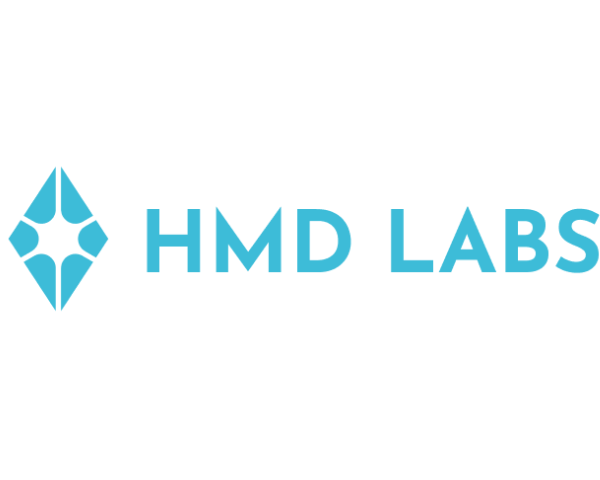
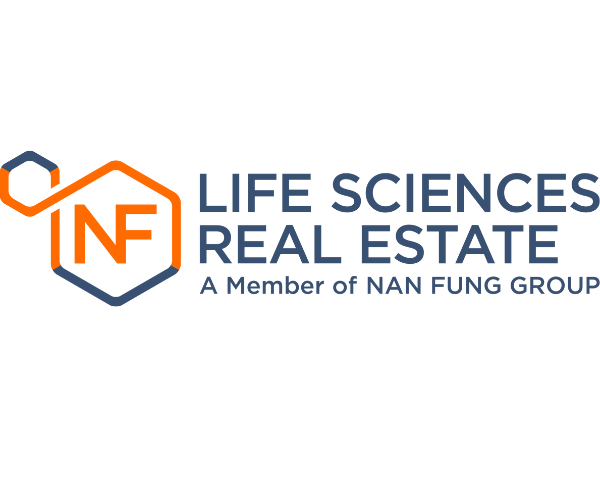
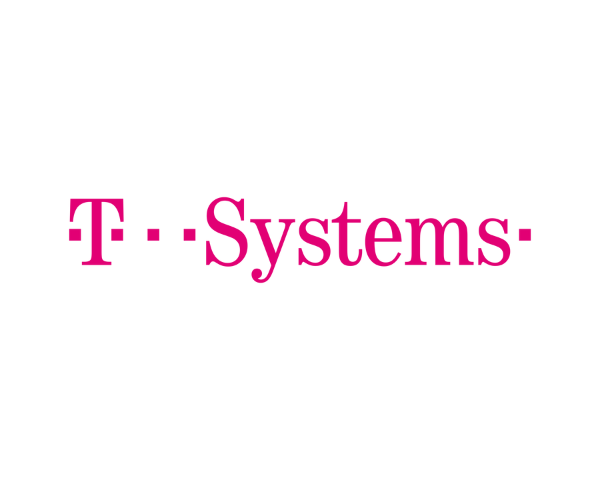
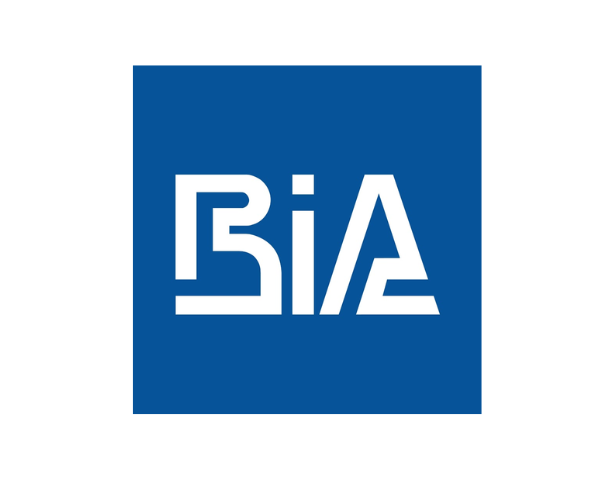
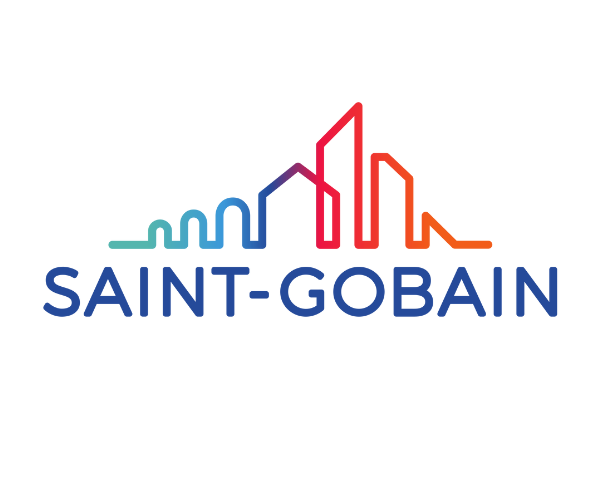
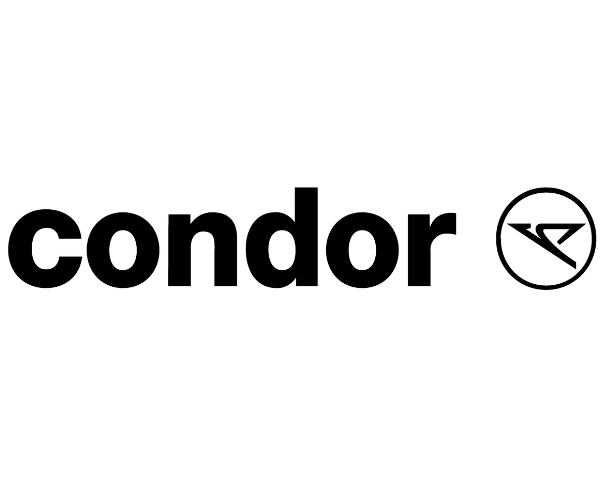
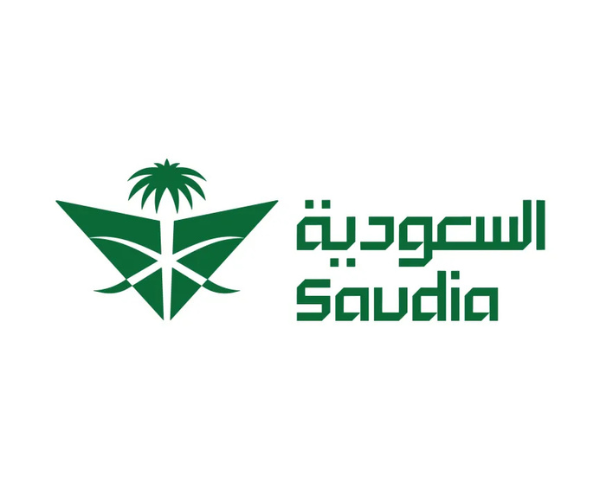
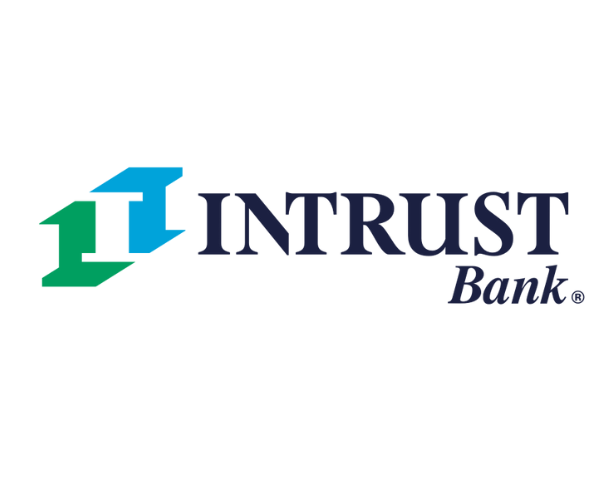
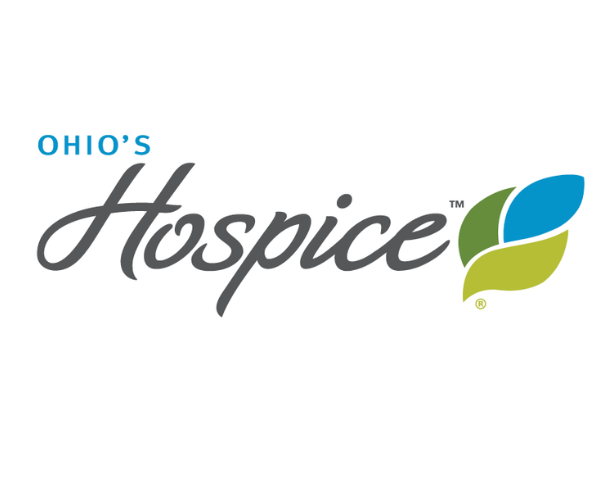
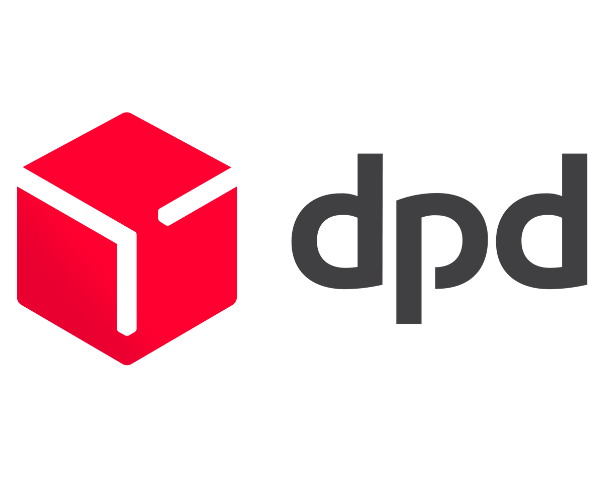
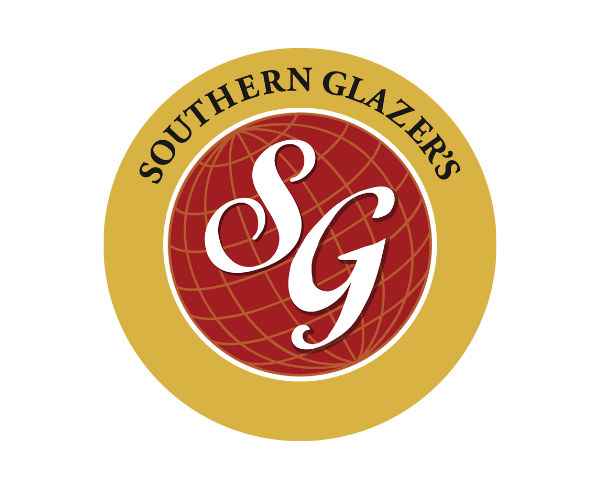
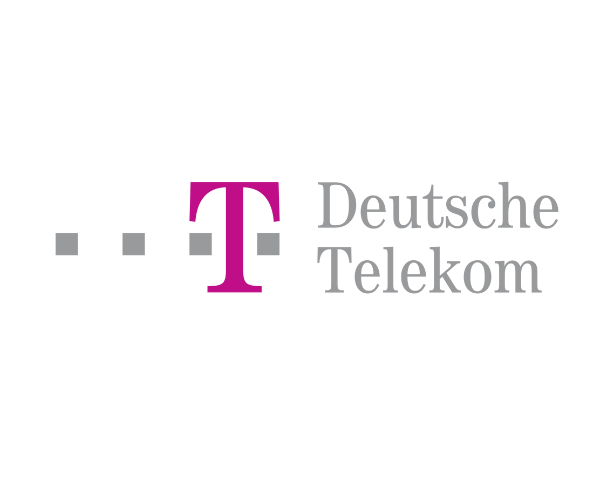
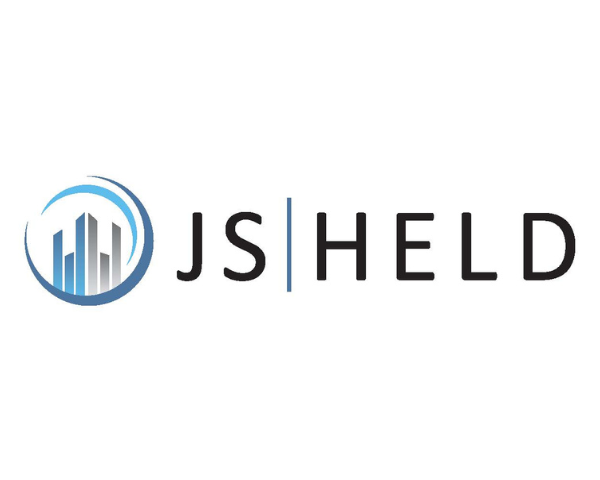
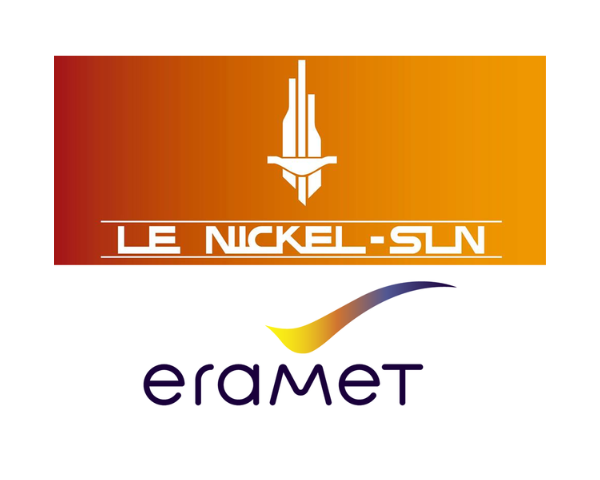
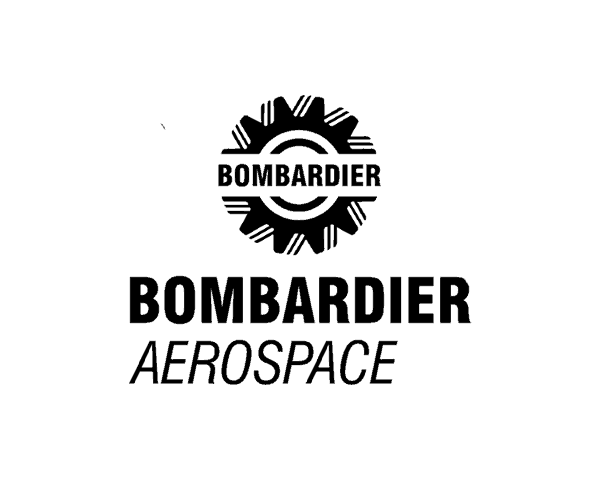


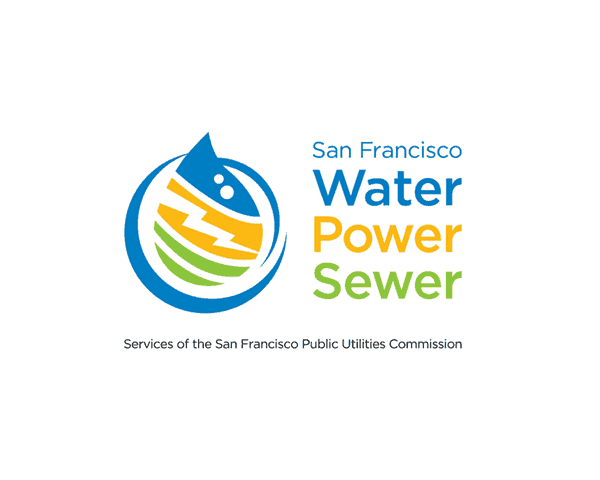
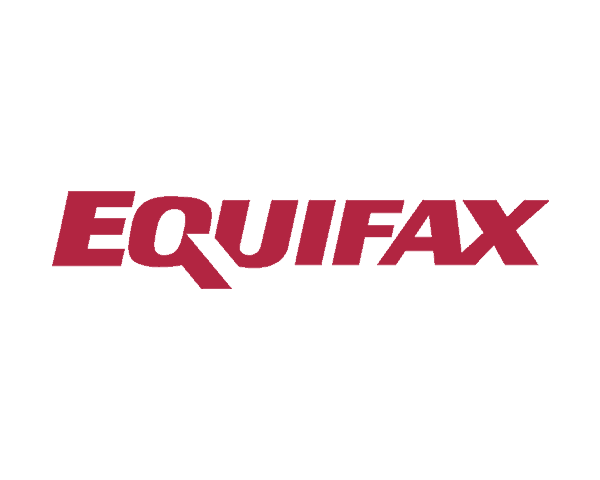
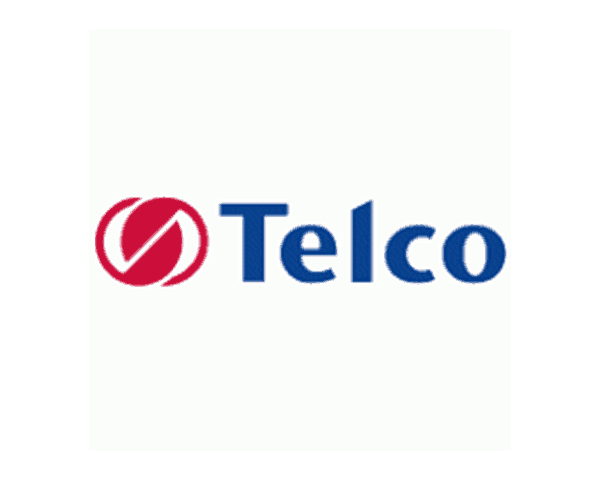
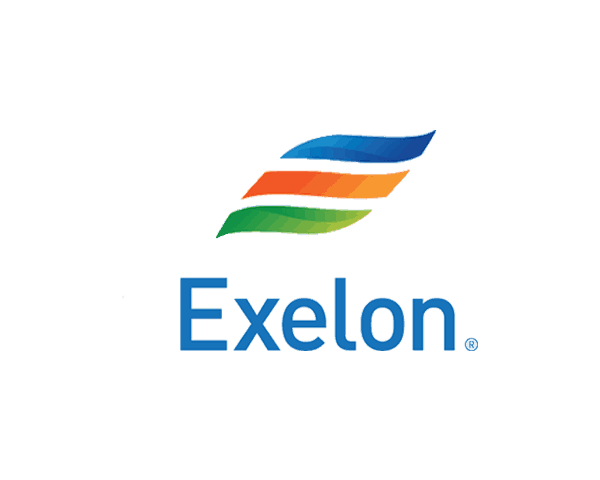
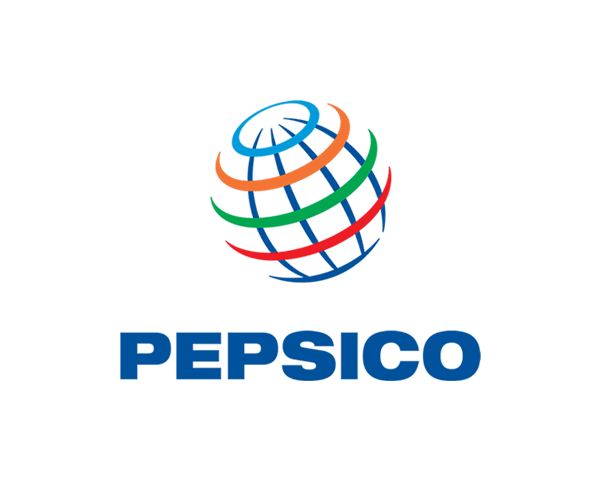
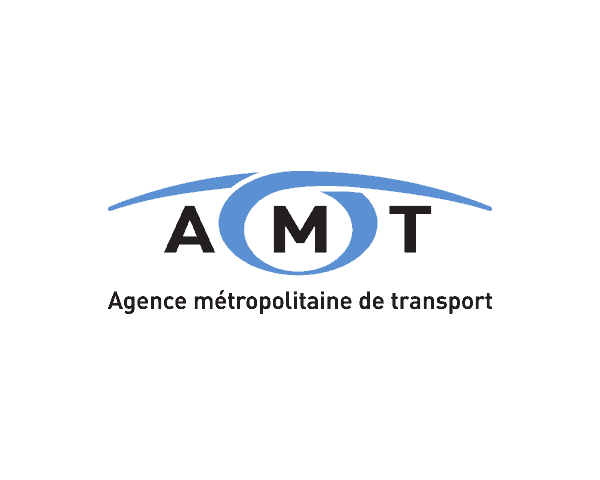
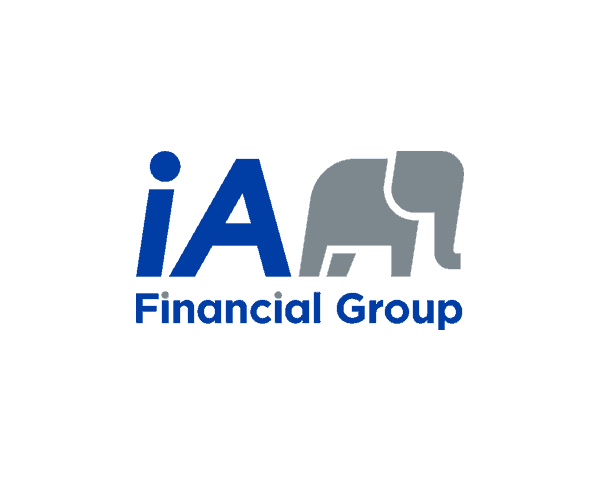
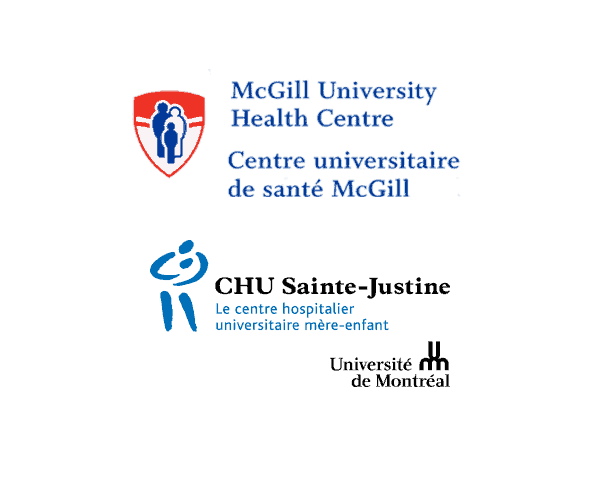
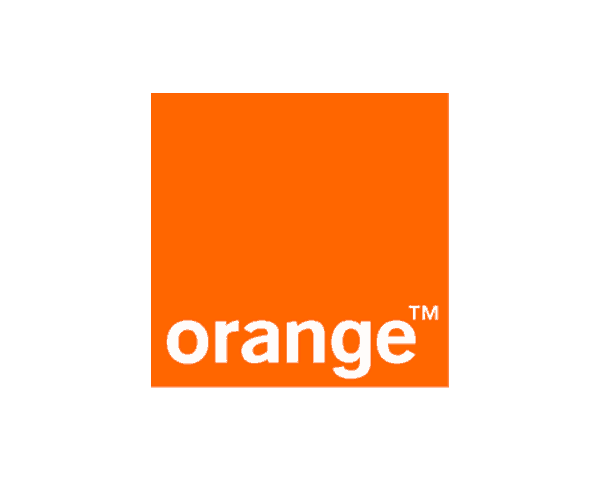
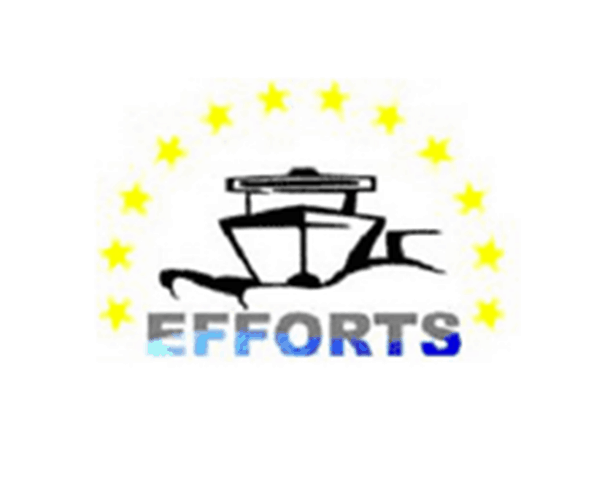
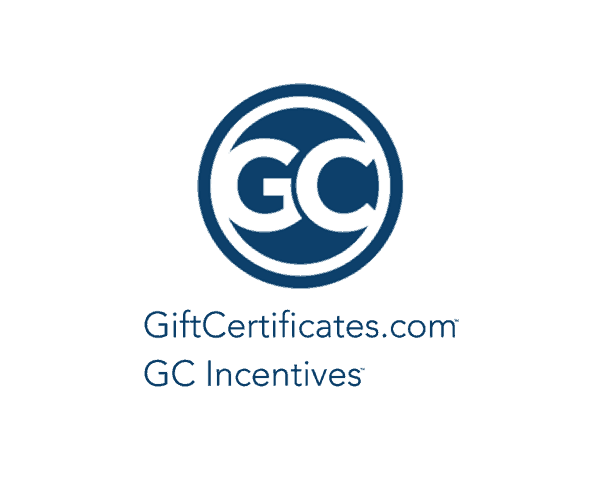
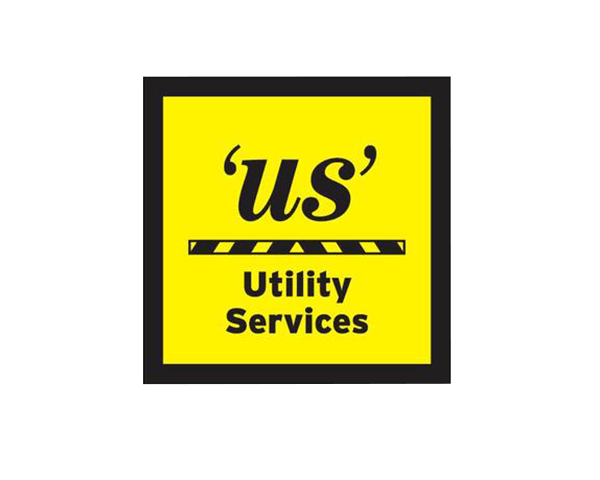